- September 21, 2022
- No Comment
- 14 minutes read
ISRI, APR revise plastic scrap specifications – Waste Today Magazine
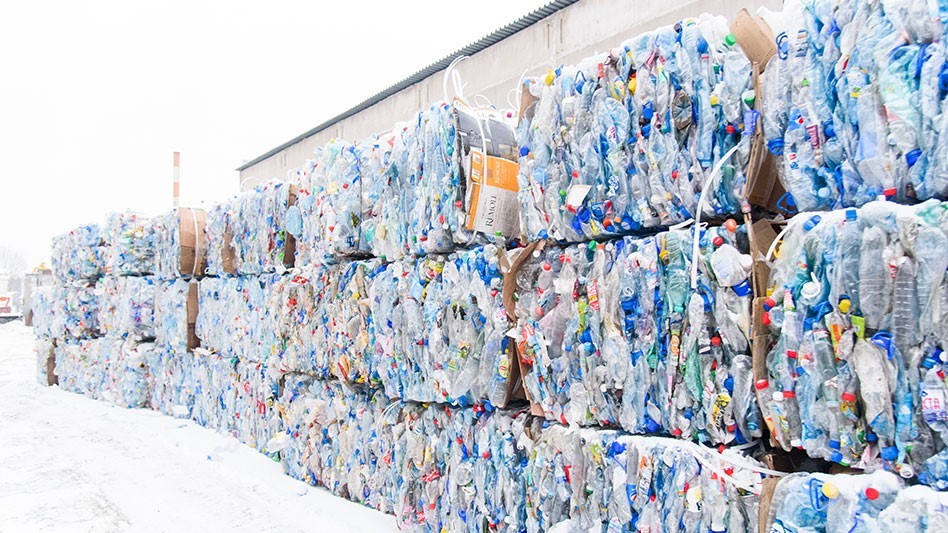
The two industry associations have approved changes to the ISRI Scrap Specifications Circular and Association of Plastic Recyclers Model Bale Specifications.
The Washington-based Institute of Scrap Recycling Industries (ISRI) and the Washington-based Association of Plastic Recyclers (APR) have updated both the ISRI Scrap Specifications Circular and APR Model Bale Specifications with revised recycled plastics specifications.
According to a news release from ISRI, these specifications were approved at the ISRI board and governance meetings July 14 as well as by the APR board of directors Aug. 2. ISRI says the specification updates “are intended to more accurately reflect the recycled plastic materials currently being traded in the marketplace.”
Since ISRI last updated recycled plastics specifications for the ISRI Scrap Specifications Circular, ISRI says technological innovations, such as optical sorters, robotics and artificial intelligence, have enabled recyclers to sort and process plastics more effectively. However, ISRI adds, evolving packaging and recycling streams require that ISRI and APR continually update bale specifications based on those changing designs.
ISRI says the specifications updates also highlight changes to the recycling stream that came as a result of the pandemic. The increased use of disposable face masks and medical equipment caused these nonrecyclable materials to enter the recycling stream, and ISRI says these specifications clarify that these nonrecyclable materials are not acceptable for recycling.
The updated specifications also address the increased use of batteries in consumer products. ISRI says the updated specifications clarify that batteries should not be placed into recycling streams by classifying them as disallowed contaminants in all plastics bale specifications.
Additionally, APR updated its APR Model Bale Specifications with revisions for recycled plastics specifications. According to ISRI, APR’s updated specifications provide guidelines for recycling market acceptance of various postconsumer, including some postcommercial, recycled plastic bales. The updates are not intended to replace the specifications of individual buyers that may allow or prohibit different contents or bale sizes.
Kate Eagles, program director at APR, says the specification update process involved working with APR’s North American plastics reclaimer members to review existing specifications and discuss any updates to desired materials and tolerable (allowable at low levels) versus prohibited contaminants, with a focus on providing as much clarity as possible to help facilitate quality material. She says APR also looked to add consistency across model specifications where possible in terms of shared introductory text, category headers, contaminant lists and general terminology used.
As a result of these updates, APR’s Model Bale Specifications now feature three polyethylene terephthalate (PET) model bale specifications: PET bottles without thermoforms; PET bottles with thermoforms; and PET thermoform only. Eagles says the “PET bottles with thermoforms” is a new model bale specification.
APR also adjusted the names of a few of the model film specifications to accurately reflect the specification content. In addition, APR expanded the “check with your buyer” section on model specifications, such as high-density polyethylene color, to reflect reclaimer-acknowledged differences in material acceptance.
ISRI President Robin Wiener says these changes resulted from “two years of work” by volunteers in ISRI’s Plastics and Nonferrous divisions.
“The ISRI Specs Circular is a living document representing the dynamic recycled materials industry,” she says. “Additionally, I am grateful to our partnership with the Association of Plastic Recyclers, which allowed us to work together to harmonize our specifications across all segments of the industry.”
“The APR was pleased to collaborate with ISRI to ensure consistency across the plastics recycling industry,” says Steve Alexander, president and CEO of APR. “These model bale specifications facilitate greater understanding of the packaging / products commonly accepted by reclaimers for recycling and also provide insight for the broader marketplace and value chain.”
The amended zoning ordinance will expand organics processing and composting options for area residents.
Board supervisors in San Diego County, California, voted unanimously Sept. 14 to amend an organic materials zoning ordinance to provide more options for community gardeners, farmers, commercial composters and residents, reports Times of San Diego.
The amended zoning ordinance (ZO) will allow organic material processing or composting to occur in more areas of the unincorporated county. According to the county’s website, this will be made possible by:
All of the changes listed for this project are voluntary, says the county. The new ordinance will not mandate or require anyone to compost or accept organic materials. The board’s vote also establishes a standalone zoning ordinance for organic materials management, amends a section on animal waste processing and develops a zoning verification permit for organic materials management.
The ordinance update project is part of a variety of plans and initiatives to “reduce San Diego County’s greenhouse gas emissions, make the best use of local natural resources and reduce the need for new landfills.” A key element to these plans is a waste diversion goal established by the board in 2017, which set an initial waste diversion goal of 75 percent by 2025.
In 2018, the county’s Climate Action Plan (CAP) increased the waste diversion goal to 80 percent by 2030.
Achieving this goal, the fourth-largest emission reduction measure in the 2018 CAP, would account for nearly 9 percent, or 79,052 metric tons of carbon dioxide equivalent, of the total emission reductions needed for 2030.
Qnergy has installed its PowerGen5650, which uses Stirling engine technology to abate methane and create clean energy, at the Midshore I Landfill in Easton, Maryland.
Qnergy Inc., Ogden, Utah, a methane abatement solutions provider and a manufacturer of clean, reliable, electric power using Stirling engine technologies, has announced its first landfill deployment to abate methane, create clean electrical energy and generate voluntary carbon credits.
Working with Maryland Environmental Service (MES) and Maryland Energy Administration’s Open Energy program, Qnergy installed its PowerGen5650 at the Midshore I Landfill in Easton, Maryland. The PowerGen5650 captures and converts low methane landfill biogas into electricity that will deliver up to 5.6 kilowatts of power for onsite operational use along with reduced energy costs from otherwise flared gas.
MES operates the landfill in Easton and one in Ridgely, Maryland, on behalf of Caroline, Kent, Talbot, and Queen Anne’s counties, as part of an 80-year solid waste agreement.
“We are excited to expand our methane abatement program to landfills,” Qnergy CEO Ory Zik says. “The Inflation Reduction Act and EPA focus on converting methane pollution into useful energy, and this is where our generators are the best system of emission reductions.”
MES Executive Director Charles Glass says the installation will help reduce methane emissions and help the landfill meet the state’s greenhouse gas emissions (GHG) standards.
“The installation of the Qnergy generator is the first step toward demonstrating the ability to use an otherwise lost byproduct at municipal solid waste landfills,” he says.
The project demonstrates an alternative to flaring and that even lower concentration landfill biogas methane can be converted into electricity and heat and reduce GHG emissions.
“As the first completed project under our recently launched Open Energy Grant Program, we are excited to know [how] the benefits will help to leverage the state’s landfills, promote clean energy and reduce greenhouse gas emissions,” Maryland Energy Administration Director Mary Beth Tung says. “We look forward to seeing replicas of this project on landfills across Maryland that support a variety of clean energy technologies.”
Related stories: Turning gas into cash | Ohio landfill to expand gas production
According to a GoFundMe created by his family, Donnie Cooper “broke both femurs, his ribs… and [has] a collapsed lung” from the incident.
A collection truck driver for Stevens Disposal and Recycling, based in Petersburg, Michigan, is in critical condition after being struck by a car while on the job, reports WTVG.
The victim, Donnie Cooper, is currently in an intensive care unit in a medically induced coma. According to a GoFundMe created by his family, Cooper “broke both femurs, his ribs… and [has] a collapsed lung” from the incident. While the total extent of his injuries is not known yet, the family says he has severe head trauma and will undergo a procedure for internal bleeding.
“Just slow down, like, literally my boyfriend is fighting for his life, and I don’t even know if he’s going to make it,” Cooper’s girlfriend, Jody, told WTVG.
She adds that the driver who collided with Cooper has been identified and stayed at the scene following the accident, however; the family does not know specifics such as how fast the driver was going.
“The state of Michigan has the move over law which requires cars to slow down,” Kevin Shipman, manager of customer relations and business development for Stevens Disposal, told Fox 2. “Unfortunately, I don’t think it is strong enough meaning you only have to slow down by 10 miles per hour. They could do more.”
This is believed to be what happened during the Sept. 15 collision. Although the road Cooper was on in Monroe, Michigan, is residential, the speed limit there is 55 miles per hour.
As reported by Fox 2, Stevens Disposal is working to prevent tragedies like this from happening in the future by using more automated garbage trucks.
Cooper’s family is accepting donations to help pay for rent, food and monthly bills in the aftermath of the accident. To visit the GoFundMe, click here.
The upgrade and expansion of the New Philadelphia, Ohio, plant positions the company to meet demand as the truck industry transitions to CNG and electric vehicles.
Proving that large-scale manufacturing and innovation are alive and well in America’s heartland, Battle Motors, New Philadelphia, Ohio, has announced the company’s expanded production facility is open and fully operational.
A game-changer for the company, the factory’s size has increased significantly—from 125,000 square feet to 325,000 square feet—or more than five football fields. Located in New Philadelphia, the facility is where Battle Motors manufactures diesel, clean natural gas (CNG) and electric vehicles (EVs) for vocational vehicles, including waste collection trucks.
Founder and CEO of Battle Motors, Michael Patterson, says the plant’s expansion is the “most ambitious” project the company has undertaken.
“We have made the investment in the expansion of the physical plant, acquired the right technology, and most importantly, have made a commitment to the people of Central Ohio by already adding 200 employees to our workforce and creating high-tech jobs at a truly momentous time,” he says. “It’s game on.”
The modernized facility will maximize the throughput of the company’s multiple production lines and transform operations as Battle Motors scales up to meet the demands of the evolving transportation landscape. From additional production lines, shipping bays and receiving docks to the latest technologies used for fabrication, paint application and vehicle assembly, Battle Motors hopes to lead the heavy-duty truck industry in the nationwide deployment of EVs.
The company invested $32 million in the facility to jumpstart fabrication, production capacity and vehicle delivery. The investment enables the team at Battle Motors to manufacture its full line of trucks with innovative feature sets including a best-in-class powertrain paired with the Battle Motors “Smart Cab,” featuring a digital instrument cluster and proprietary software, RevolutionOS.
“Reaching this milestone is definitely an achievement we’re very proud of,” Battle Motors Chief Operating Officer Cody Boggs says. “Our team of local labor and contractors minimized the disruption that can be expected with an expansion of this size, and our production numbers throughout have been really impressive. Working within the limitations of our original factory, we still hit record numbers month-over-month, reaching our 2021 [production goal] by July of this year.”
Battle Motors executives are more optimistic than ever about future production, which will be driven by the new facility’s continuous assembly flow and automation upgrades and powered by vertical integration capabilities including 3D printing, laser cutting and CNC machining.
The company owns additional acreage adjacent to the new facility where the build-out of new assets is planned, including research and development and prototype fabrication spaces, as well as a test track.